The usage of this emblematic stone of the Loire valley dates back to the Gallo-Roman period, like the first open quarries can prove. Thanks to the Loire navy, it has crossed the borders of the region.
What is the secret of its success? Tufa is a porous stone, both light and solid at the time. Its velvet-soft texture makes it feel more like a fabric than a rock. Its light and warm colours give a special cachet to the villages and towns of the Loire valley.
Most of the time, it is used as a cut stone, especially for visible façades, quoins and frameworks of residences. The softness of the stone also gives a lot of creative space to sculptors’ art. This is why cornices, mouldings, pilasters, capitals and friezes made of tufa can be observed on many buildings, on the façades of residences and the most prestigious castles.
The omnipresence of tufa and the sculptured or moulded elements give a visible architectural unity to the region; even if construction methods might vary locally. Around Richelieu, for example, limestone rubble (small construction stones) replaces the cut stone. The architectural influence of the near Poitou is also visible on roofs which sometimes are covered with so-called “tuiles canal” (half-round tiles mostly made of terracotta) instead of slate.
All over the territory, sophisticated tufa constructions witness a know-how grown over centuries. A large range of professions has developed around this sector, such as stone cutting for the decoration of contemporary constructions and restoration of old buildings. Since tufa has been abandoned to more modern construction materials, the main challenge is the transmission of this ancient know-how and the rehabilitation of the most emblematic historical monuments of the region: the Fontevaud abbey, the collegiate church of Candes-Saint-Martin, the castles of Azay-le-Rideau, Saumur, Chinon, Villandry, etc.
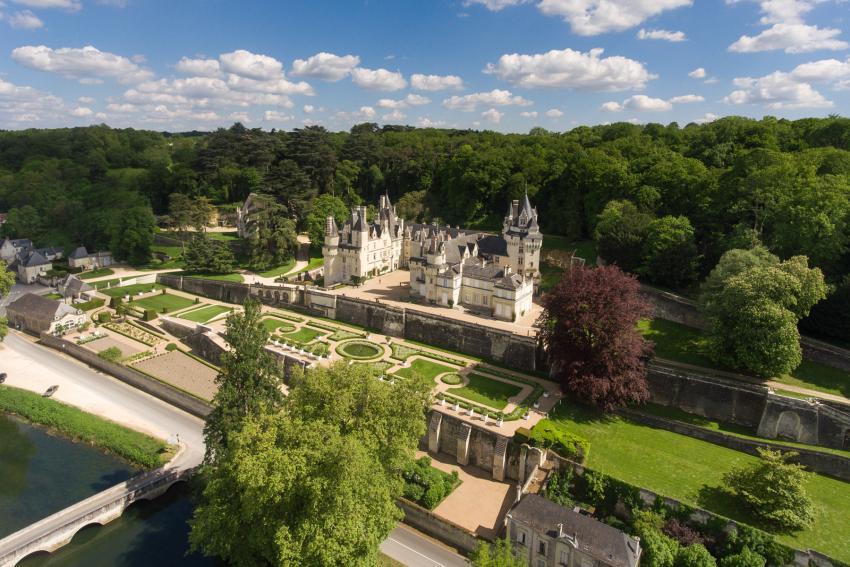
Geology and tufa extraction
Touraine tufa, also called Saumur tufa, was largely used over centuries, especially for the construction of the big castles of the Loire during the Renaissance. It is still used for the restoration of old monuments (from Orléans to Saint-Nazaire and from Poitiers to Rennes), as well as for rehabilitation works of old structures, mainly houses. Tufa is a limestone constituted by the accumulation and settlement of marine sediments. Fossil particles cement and form rocks which are over 90 million years old today. It can be up to 40 m deep! Tufa was extracted by digging galleries in the hillsides. Quarries brought out huge stone blocks which were then pre-cut on spot and carted to the river. On the docks, the blocks were washed by overflows before being loaded into scows for shipping on the Loire. This extraction method is the cradle of troglodytism: little by little, quarrymen have transformed disused galleries for their private use. There are three types of tufa on the territory:
- The white tufa is the most noble work stone. It is used for building monuments and rich mansions.
- The yellow tufa is the sandiest one. In Touraine, it is used for building rural houses, maintaining the dykes and constructing the foundations of certain buildings.
- The grey tufa with its bluish glints can be found between Saumur and Gennes. It is the most fragile one and was used for the production of hydraulic lime.
The extraction is almost completely stopped in the 1950s. It starts again in a quarry of the Saumur region in 1964 on the request of an architect from the “Monuments Historiques” (national heritage site in France) to allow the renovation of the Fontevraud abbey.
Stonework professions
The quarries
Tufa extraction is hard and dangerous work only done by the quarrymen (also called “perreyeux” in some regions). During a long time, many of them are peasants, working for extra money during the winter. But as the demand rises in the 19th century, tufa extraction becomes more professional: in 1850 in Montsoreau, 500 out of 800 inhabitants are quarrymen! But in the early 20th century, new competitive building materials lead to the decline of the tufa activities and quarries progressively shut down.
The stone mason
The stone mason cuts the tufa block to make it regular and of a certain size: he is the one who cuts the so-called “pierre de taille” (cut stone) which will be used to build walls, vaults, door and window frameworks, staircases, … He uses a working drawing in order to know the way he should cut the block. So, a stone mason knows all about technical design and drawing, different trends in architecture, … On the Park territory, tufa is everywhere. Technical cut know-how and tools are developed to work the stone. Stone masons use a dresser, for example, a sort of plane with steel blades, for surface finishing on soft stone elements.
The sculptor
The tufa stone is easy to work with. Most of the buildings were made of tufa, so, the sculptors of the region had a lot of space to express themselves: bas-reliefs where the pattern hardly stands out from the background; high reliefs where the sculpture is partly attached to the background; and statues. The sculptor creates his objects cutting the stone with scissors based on a sketch.
The challenges of rehabilitation work
It is not easy to rehabilitate ancient buildings with today’s know-how and constraints. Perfect knowledge of stonework and local traditional methods are a must. For example, tufa is a porous stone and therefore vulnerable to freeze and humidity. It is important to take precautions to prevent the stone from bursting.
Today, the improvement of energy efficiency of old buildings is a national priority. But the isolation of old tufa constructions is a real technical challenge for the building professionals. Unsuitable reconfigurations can degrade the building quality and cause problems with humidity, with the heat regulation in winter and more generously with the stone itself (e.g. mildew).
Little by little, a true know-how of ecological rehabilitation and energy renovation is developed, fully respecting the specificities of tufa. The comfort of old houses is improved while letting the tufa breath. Building companies have a leading role to play: they pass on knowledge about techniques, for example via the so-called “compagnonnages” (companionship and apprenticeship) networks.